Amazon Scout Home Base
Amazon Scout Launch Video (January 2019)
My first job upon graduating from the University of Washington with my master’s degree in mechanical engineering was at Amazon. I returned to Scout, Amazon’s ground-based delivery robotics program, following an internship the previous summer. My manager assigned me to the Home Base project, which was the supporting infrastructure that allowed the robots to charge overnight and offload any data they had gathered.
Approximately a dozen first generation Home Base units were in use when I started at Scout in September 2021. These units were essentially buildings the size of a parking space. The cost to build, permit, and deploy a Home Base was measured in the hundreds of thousands of dollars. This expense was not justifiable for a structure that only held 20 robots, but the project was not a waste. Building, landing, and operating out of these units gave us a wealth of information.
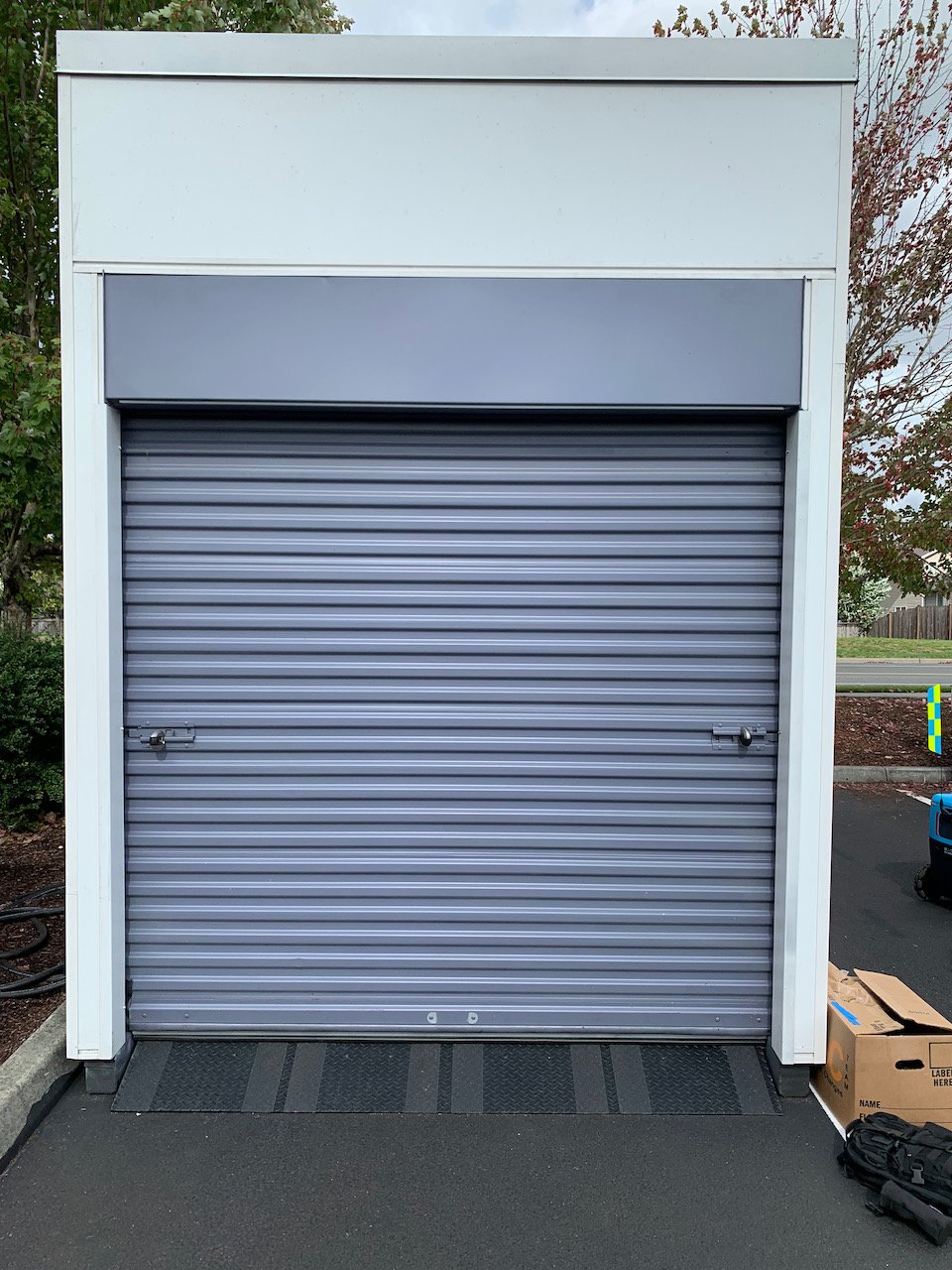
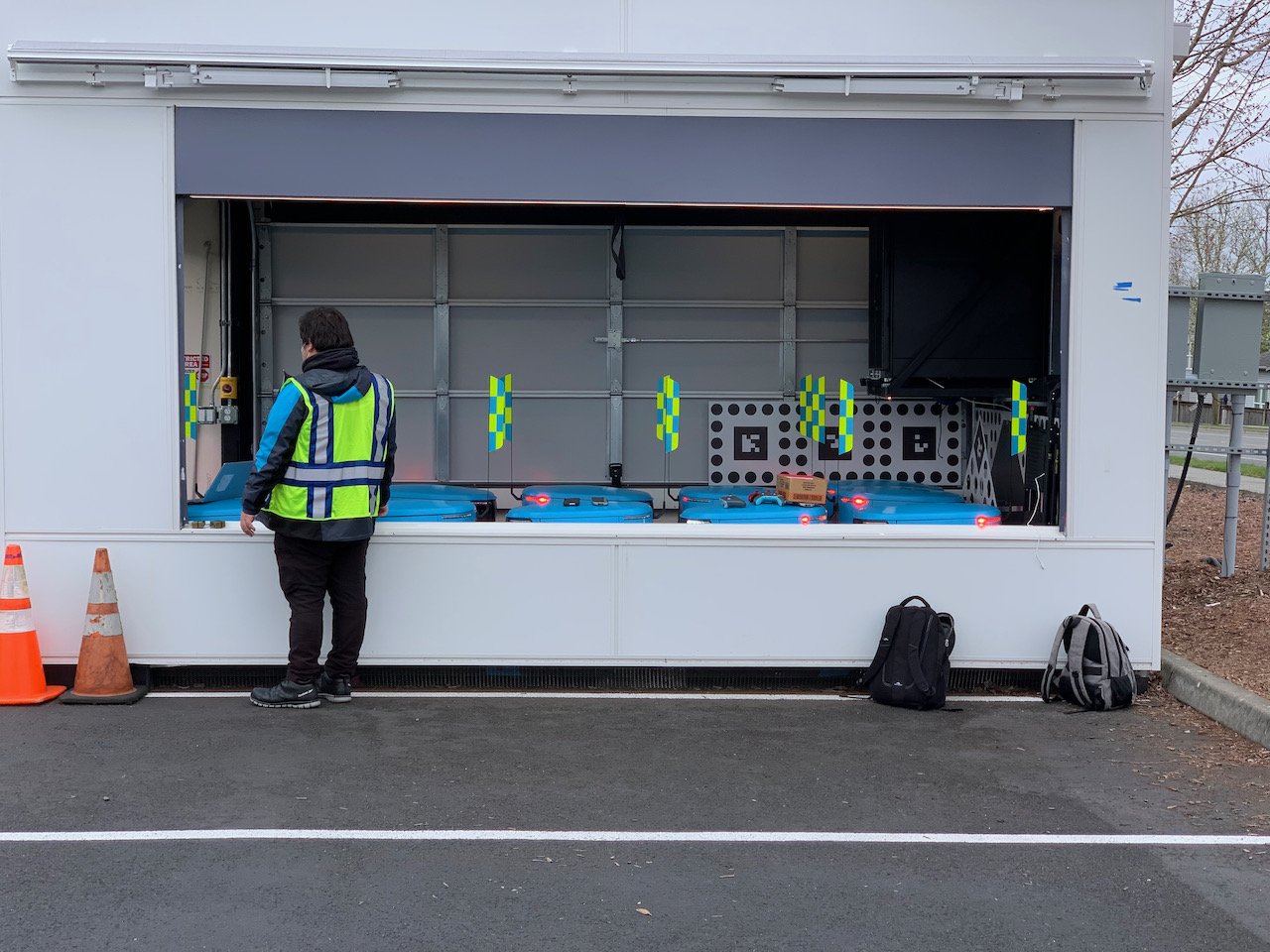
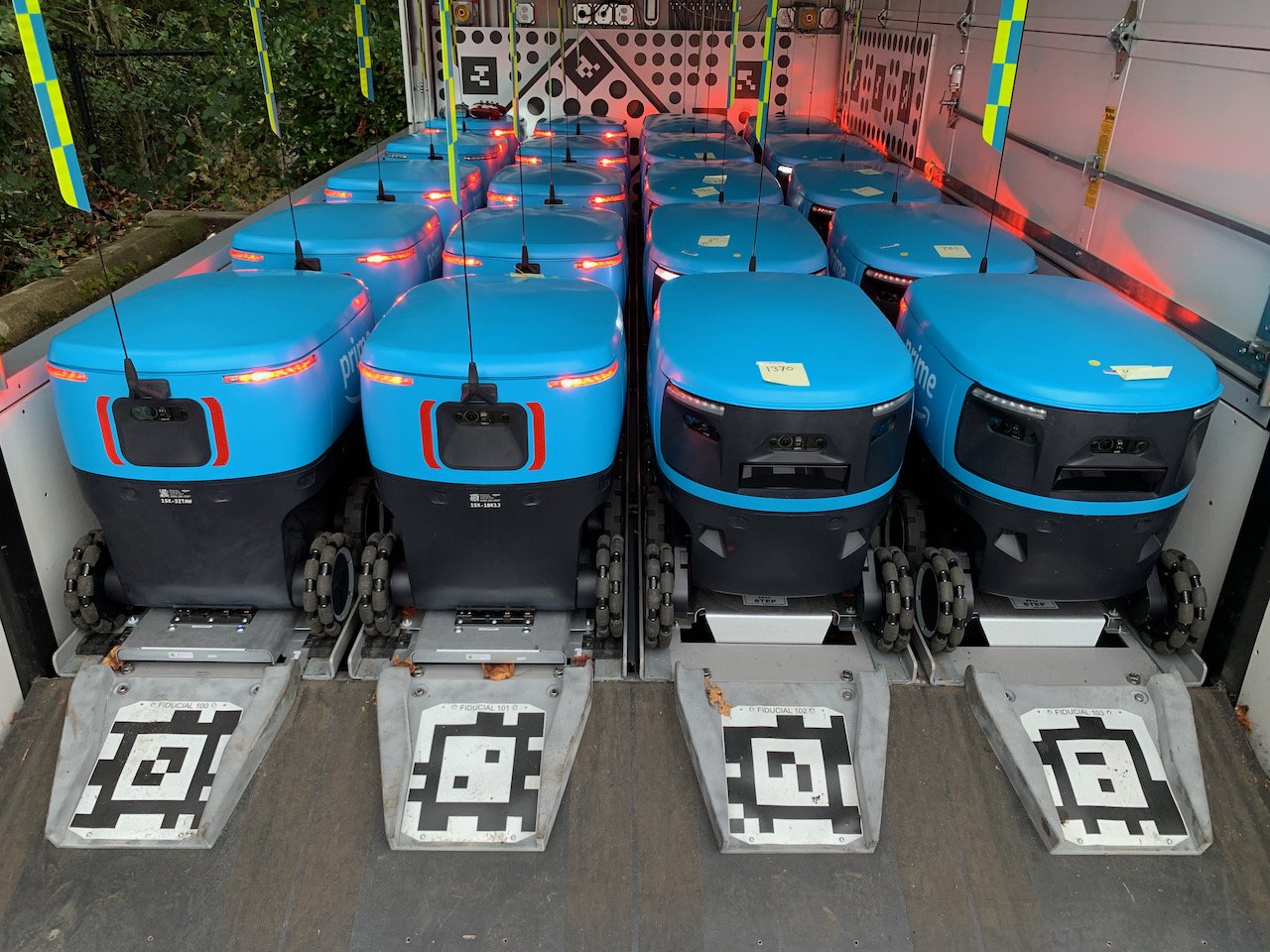
The most important takeaway from our experience with these first generation units was a list of questions to be answered. How could we speed up the permitting process? How could we minimize the amount of on-site assembly? What was the best layout for speedy operations? The next generation of Home Base needed to answer these and other questions and do so at a much lower price.
Rather than design a different prototype to answer each question, I proposed that we design a system consisting of interconnecting units that could be assembled in various configurations. My coworkers agreed that a modular system was the best approach, so we got to work. The resulting design was for pod capable of handling the charging and data offload needs of one robot. These pods could be lined up front-to-back, side-to-side, or some combination of the two to create a customized configuration for the needs of the site.
Modular unit with full environmental protection
Modular unit with security channel (vertical piece on right) but no environmental protection.
The electrical architecture was modular as well, supporting a range of power requirements. If only a handful of robots were needed, the system could plug into a standard wall outlet. If the site needed to charge many robots, the electrical system could be connected to utility power. Amazon deemed our design to worthy of filing for patent protection. If it is granted, it will be the first patent on which I am listed as an inventor.
This project was the first one in which I was designing a whole system alongside other engineers. Rather than treat all interfacing parts as fixed, I was able to influence the design of the overall system in addition to the parts that I focused on. While much of my design work was independent, I regularly checked with my coworkers to ensure that my design choices worked with their part and vice versa.
This project was also a good example of the importance in trying to account for all design considerations from the very beginning. For example, we worked together with the electrical team to determine our system design rather than try to force the electrical engineers to work around an existing mechanical design. Although this increased the initial workload and design complexity, it spared us any significant redesign later in the process and allowed for a better final product.